 Книжкові видання та компакт-диски  Журнали та продовжувані видання  Автореферати дисертацій  Реферативна база даних  Наукова періодика України  Тематичний навігатор  Авторитетний файл імен осіб
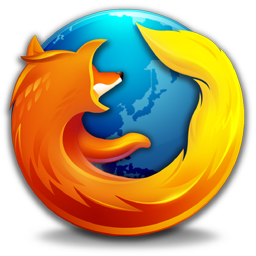 |
Для швидкої роботи та реалізації всіх функціональних можливостей пошукової системи використовуйте браузер "Mozilla Firefox" |
|
|
Повнотекстовий пошук
Пошуковий запит: (<.>A=Kalchenko D$<.>) |
Загальна кількість знайдених документів : 7
Представлено документи з 1 до 7
|
1. |
Kalchenko V. Modular 3D modeling of ends bilateral grinding process by wheels with conical calibrating sections [Електронний ресурс] / V. Kalchenko, V. Kalchenko, О. Slednikova, D. Kalchenko // Вісник Тернопільського національного технічного університету. - 2016. - № 4. - С. 82-92. - Режим доступу: http://nbuv.gov.ua/UJRN/tstub_2016_4_10
| 2. |
Kalchenko D. Theoretical and experimental study of double-sided grinding process of round face ends by orientated wheels with calibrating sections [Електронний ресурс] / D. Kalchenko // Scientific journal of the Ternopil national technical university . - 2018. - № 1. - С. 100-112. - Режим доступу: http://nbuv.gov.ua/UJRN/tstub_2018_1_13
| 3. |
Lytvyn O. Investigation of the process of double-sided grinding of torches of pushers with different diametrers [Електронний ресурс] / O. Lytvyn, D. Kalchenko // Технічні науки та технології. - 2018. - № 2. - С. 86-93. - Режим доступу: http://nbuv.gov.ua/UJRN/tnt_2018_2_10 У верстатобудуванні, автомобілебудуванні, сільськогосподарському машинобудуванні, виробництвах, де необхідне забезпечення високої точності поверхонь деталей з різними діаметрами торців, потрібно дотримуватися високих вимог до якості, що висуваються до геометричних розмірів, шорсткості та точності формоутворення.
| 4. |
Kalchenko V. Development of a model of tool surface dressing when grinding with crossed wheel and cylindrical part axes [Електронний ресурс] / V. Kalchenko, V. Kalchenko, O. Kalchenko, N. Sira, D. Kalchenko, V. Morochko, V. Vynnyk // Восточно-Европейский журнал передовых технологий. - 2020. - № 3(1). - С. 23-29. - Режим доступу: http://nbuv.gov.ua/UJRN/Vejpte_2020_3(1)__4 Проведено тривимірне геометричне моделювання процесу формоутворення циліндричних деталей у процесі шліфування зі схрещеними вісями її та круга. Шліфування валів, які широко використовуються у автомобіле-, верстатобудуванні, та валків стрічкопрокатних станів здійснюється за одну установку орієнтованим широким абразивним кругом. На базі отриманої просторової моделі формоутворення та зняття припуску досліджено розподіл припуску вздовж різальної ділянки інструмента у процесі шліфування орієнтованим інструментом. Показано, що на периферійній різальній ділянці шліфувального круга суміщаються чорнова, чистова обробки та калібрування. Розроблено модульну тривимірну модель правки периферійної ділянки шліфувального круга однокристальним алмазним інструментом у процесі шліфування зі схрещеними вісями інструмента та деталі з використанням уніфікованих модулів правлячого інструмента, орієнтації та формоутворення. На базі наданої моделі проведено дослідження геометричної точності формоутворення периферійної ділянки інструмента після його правки. З метою отримання необхідної мікрогеометрії та різальних властивостей абразивних кругів відповідно до особливостей процесу обробки валків стрічкопрокатних станів орієнтованим інструментом запропоновано правку зі зменшеною подачею правлячого інструмента до калібрувальної ділянки. У цьому випадку величина подачі правлячого однокристального інструмента залежить від величини припуску. Різна подача правлячого інструмента забезпечує різну розвиненість різальної периферійної ділянки інструмента. Це, своєю чергою, збільшує інтервали між правками шліфувального круга, який працює у режимі затуплення. А отже, підвищується стійкість і зменшується собівартість обробки. Впровадження запропонованого способу правки кругів за однопрохідного шліфування зі схрещеними вісями інструмента та циліндричної деталі забезпечить високіточність, якість оброблених поверхонь, а також значно підвищить ефективність і продуктивність процесу обробки. Розроблений спосіб правки можна застосовувати для процесів круглого шліфування зі схрещеними вісями оброблюваної деталі та абразивних кругів.
| 5. |
Kalchenko V. Development of the single-setup milling process model of the shaft support necks and cams [Електронний ресурс] / V. Kalchenko, V. Kalchenko, N. Sira, O. Kalchenko, D. Kalchenko, V. Vynnyk, V. Morochko // Восточно-Европейский журнал передовых технологий. - 2020. - № 4(1). - С. 48-54. - Режим доступу: http://nbuv.gov.ua/UJRN/Vejpte_2020_4(1)__7 Запропоновано тривимірне геометричне моделювання процесів зняття припуску та формоутворення опорних шийок і кулачків розподільних валів при фрезеруванні зі схрещеними вісями інструмента та деталі. Фрезерування розподільних валів, які широко використовуються в автомобіле-, тракторо-, суднобудуванні та інших галузях промисловості, здійснюється за одну установку фрезою зі схрещеними вісями її та деталі. Величина кута повороту фрези вибирається з умови забезпечення необхідної шорсткості обробленої поверхні та регулюється подачею. При цьому висока продуктивність обробки забезпечується збільшенням частоти обертання розподільного валу. Розроблено спосіб фрезерування опорних шийок і кулачків, де обробка ведеться фрезою, висота якої є меншою довжин оброблюваних поверхонь. При обробці на прохід основний припуск знімається торцем чотиригранної чорнової твердосплавної пластинки, а чистова обробка здійснюється розвантаженою периферією чистової пластинки з металокераміки. Такий розподіл у припуску підвищує продуктивність і точність обробки, а можливість повороту чорнової пластинки забезпечує економію матеріалу та знижує собівартість обробки. В процесі фрезерування криволінійної поверхні кулачка розподільного валу глибина врізання вздовж оброблюваного профілю завжди більше величини припуску, що знімається. Це стає причиною зниження точності та продуктивності обробки. З метою виключення вказаної проблеми запропоновано стабілізувати глибину різання та подачу вздовж контуру за нерівномірного обертання деталі. Рівномірність глибини різання та подачі вздовж криволінійного контуру кулачка досягається одночасним вертикальним і поперечним переміщеннями фрези та нерівномірним обертанням розподільного валу. При фрезеруванні криволінійної поверхні кулачка, центр якої не збігається з центром розподільного валу, здійснюється нерівномірне обертання останнього та синхронні вертикальне та поперечне переміщення фрези. При обробці ділянки кулачка, центр якої збігається з центром розподільного валу, фрезі надається лише обертання.
| 6. |
Kalchenko V. Building a model of dressing the working surfaces of wheels during the two-side grinding of round end faces at CNC machines [Електронний ресурс] / V. Kalchenko, V. Kalchenko, A. Kolohoida, A. Yeroshenko, D. Kalchenko // Eastern-European journal of enterprise technologies. - 2022. - № 1(1). - С. 86-93. - Режим доступу: http://nbuv.gov.ua/UJRN/Vejpte_2022_1(1)__12 This paper reports the spatial mathematical modeling of the process of dressing the working surface of grinding wheels for implementing the double-sided grinding of the ends of cylindrical components. Parts with high-precision end surfaces that are commonly used include bearing rollers, piston fingers, crosspieces of cardan shafts, and others. The geometric accuracy of surfaces is ensured by simultaneously grinding the ends at two-sided end-grinding machines with crossed axes of the part and wheels that operate under a self-blunting mode. Before starting the machining, the wheels are dressed in a working position. Moreover, the total orientation angle of the tools is selected subject to the condition of uniform distribution of allowance along the rough sections of wheels. Dressing involves a single-crystal diamond tool with a variable feed. That ensures different development of the surface of abrasive tools, which prolongs their operating time between dressings and improves overall stability. The constant size of micro irregularities at the calibration site enhances the quality of machining. The calibration site is made in the form of a straight line belonging to the plane that passes through the axis of rotation of the wheel and is perpendicular to the plane of the machined part. Based on the spatial mathematical models of the processes of removal of allowance and shape formation when dressing the wheel, the surface of the grinding wheel was investigated. Mathematical models for shaping the ends of parts when grinding with wheels with conical calibration sites have been proposed; it is shown that when applying the proposed machining scheme, there is no geometric error in the size of the part. In addition, due to the uniform distribution of the allowance along the rough area of the wheel, the quality of the surface layer of the ends of parts increases. The devised method for dressing the working surface of wheels could be used to grind the ends of non-circular components.This paper reports the spatial modeling of the dressing process of grinding wheels with a conical calibration area to enable two-sided end grinding of cylindrical parts. Components with cylindrical end surfaces are common in the industry, for example, bearing rollers, crosses, piston fingers, and others. High requirements are put forward for the accuracy and quality of the end surfaces. The most efficient is to machine them simultaneously on a double-sided face grinding machine. To improve the quality, grinding is carried out by oriented wheels. The wheel's angle of rotation in the vertical plane is chosen subject to the uniform distribution of the allowance along a working surface; this makes it possible to reduce the temperature in the cutting zone and improve machining conditions. To improve the accuracy, grinding wheels are provided with a conical calibration area whose rectilinear generatrix is in the plane passing through the axis of wheel rotation and is perpendicular to the end of the part. The minimum permissible length of the calibration area depends on the diameter of the parts being machined; that makes it possible to utilize the work surface more efficiently. Two wheels are dressed simultaneously using diamond pencils that are symmetrically installed in a part feed drum. The angular velocity when dressing the rough area of the wheel is constant, which ensures its different development, and it gradually decreases when dressing the calibration area to provide for its constant roughness. In general, this prolongs the resource of grinding wheels and the quality of machining. The wheels are given axial movement to ensure the straightness of the cone calibration area. The dressing technique reported here can be used on machines equipped with a numerical software control system and without it. It could also be applied in the machining of parts with non-round ends.
| 7. |
Kalchenko V. Building a model of the process of shaping tapered calibrating areas of wheels at the two-sided grinding of round ends [Електронний ресурс] / V. Kalchenko, V. Kalchenko, A. Kolohoida, O. Kalchenko, D. Kalchenko // Eastern-European journal of enterprise technologies. - 2022. - № 2(1). - С. 62-70. - Режим доступу: http://nbuv.gov.ua/UJRN/Vejpte_2022_2(1)__9 This paper reports the spatial mathematical modeling of the process of dressing the working surface of grinding wheels for implementing the double-sided grinding of the ends of cylindrical components. Parts with high-precision end surfaces that are commonly used include bearing rollers, piston fingers, crosspieces of cardan shafts, and others. The geometric accuracy of surfaces is ensured by simultaneously grinding the ends at two-sided end-grinding machines with crossed axes of the part and wheels that operate under a self-blunting mode. Before starting the machining, the wheels are dressed in a working position. Moreover, the total orientation angle of the tools is selected subject to the condition of uniform distribution of allowance along the rough sections of wheels. Dressing involves a single-crystal diamond tool with a variable feed. That ensures different development of the surface of abrasive tools, which prolongs their operating time between dressings and improves overall stability. The constant size of micro irregularities at the calibration site enhances the quality of machining. The calibration site is made in the form of a straight line belonging to the plane that passes through the axis of rotation of the wheel and is perpendicular to the plane of the machined part. Based on the spatial mathematical models of the processes of removal of allowance and shape formation when dressing the wheel, the surface of the grinding wheel was investigated. Mathematical models for shaping the ends of parts when grinding with wheels with conical calibration sites have been proposed; it is shown that when applying the proposed machining scheme, there is no geometric error in the size of the part. In addition, due to the uniform distribution of the allowance along the rough area of the wheel, the quality of the surface layer of the ends of parts increases. The devised method for dressing the working surface of wheels could be used to grind the ends of non-circular components.This paper reports the spatial modeling of the dressing process of grinding wheels with a conical calibration area to enable two-sided end grinding of cylindrical parts. Components with cylindrical end surfaces are common in the industry, for example, bearing rollers, crosses, piston fingers, and others. High requirements are put forward for the accuracy and quality of the end surfaces. The most efficient is to machine them simultaneously on a double-sided face grinding machine. To improve the quality, grinding is carried out by oriented wheels. The wheel's angle of rotation in the vertical plane is chosen subject to the uniform distribution of the allowance along a working surface; this makes it possible to reduce the temperature in the cutting zone and improve machining conditions. To improve the accuracy, grinding wheels are provided with a conical calibration area whose rectilinear generatrix is in the plane passing through the axis of wheel rotation and is perpendicular to the end of the part. The minimum permissible length of the calibration area depends on the diameter of the parts being machined; that makes it possible to utilize the work surface more efficiently. Two wheels are dressed simultaneously using diamond pencils that are symmetrically installed in a part feed drum. The angular velocity when dressing the rough area of the wheel is constant, which ensures its different development, and it gradually decreases when dressing the calibration area to provide for its constant roughness. In general, this prolongs the resource of grinding wheels and the quality of machining. The wheels are given axial movement to ensure the straightness of the cone calibration area. The dressing technique reported here can be used on machines equipped with a numerical software control system and without it. It could also be applied in the machining of parts with non-round ends.
|
|
|